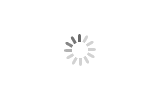
- Qingqingquan
- Shandong
- 20 days
- 300 units per month
Recover up to 90% nickel from electroplating wastewater with our dual-membrane systems. Reduce operational costs by 30% while meeting standards. Custom solutions for automotive, electronics, and jewelry plating plants.
Top-Rated Nickel Recovery Systems for Electroplating Wastewater: Dual-Membrane Tech Achieves 90% Recovery, 30% Cost Reduction"
Introduction: The double dilemma of “cost and compliance” in electroplating industry wastewater treatment
The electroplating industry accounts for 10% of the total industrial wastewater discharge, and its wastewater containing nickel, chromium, and other heavy metals will not only be subject to stringent regulation if not effectively treated, but also to hundreds of thousands of dollars in fines for exceeding the discharge standards. However, the traditional chemical precipitation method recovery rate of only 50% -70%, and the high cost of sludge treatment; ion exchange method due to the resin is easily saturated, regeneration costs are expensive, so that small and medium-sized enterprises are discouraged.
The key to break the game: how to achieve low-cost, high-efficiency, resourceful wastewater treatment through technological innovation?
I. Traditional technology vs. dual membrane separation: the ultimate duel between recovery rate and cost
1. Traditional technology “three mountains”
• Chemical precipitation method: need to add a large amount of lye, nickel recovery rate of less than 70%, and each ton of wastewater produces 0.5-1 tons of hazardous waste sludge, disposal costs up to 2,000 yuan / ton.
• Ion exchange method: resin life is short (1-2 years), the cost of regeneration chemicals accounted for more than 40% of the operating costs.
• Evaporation crystallization method: very high energy consumption (about 80kWh/ton of water), only large enterprises can afford.
2. Dual-membrane separation technology: 90% recovery rate of “black technology”
Dual-membrane technology = ultrafiltration (UF) + reverse osmosis (RO), through the two-stage membrane separation to achieve heavy metal concentration and water reuse:
• Ultrafiltration (UF): intercepts suspended solids, colloids and macromolecules in wastewater and protects the reverse osmosis membrane from contamination.
• Reverse osmosis (RO): separates water molecules and nickel ions under high pressure, and the COD of produced water is <10mg/L, which can be directly reused in electroplating cleaning process.
Core Advantages:
✅ Recycling rate breaks through 90%: far exceeding the traditional method, the annual cost savings of nickel resources exceeds 500,000 yuan (taking the electroplating plant with daily treatment of 150 tons of wastewater and nickel concentration of 50mg/L as an example).
✅ 30% direct reduction in operating costs: energy consumption is reduced by 20%, membrane life is extended to 3-5 years, and there is no need to frequently replace the resin or add precipitant.
✅ Zero-discharge potential: the concentrate can be further evaporated and crystallized to achieve nickel salt resourcing and reduce the amount of hazardous waste by 90%.
Market status: Although dual membrane technology has been included in the Catalog of Major Environmental Protection Technologies and Equipment Encouraged by the State, the market awareness is less than 15%, with little competition and huge potential.
Ⅱ. Electroplating wastewater nickel recovery equipment selection guide: how to avoid the “IQ tax”?
1. The core parameters of the equipment: the key to determining the recovery rate and life
• Membrane Material Selection: Priority should be given to the use of anti-pollution reverse osmosis membranes (e.g. Dow FILMTEC™ BW30FR-400), which can tolerate COD ≤ 100mg/L influent water and reduce the frequency of cleaning.
• System design: need to be equipped with automated cleaning devices (such as pneumatic scrubbing + chemical cleaning) and online monitoring instrumentation (conductivity, pressure, flow) to ensure stable operation.
• Modular design: suitable for small and medium-sized electroplating plants (50-200 tons per day), flexible expansion of production capacity.
2. Cost Comparison: Dual Membrane Plant vs. Traditional Precipitation Method (based on 10-year cycle)
Conclusion: The payback period for dual membrane technology is only 3 years and the long-term benefits are significant.
Ⅲ. Zero Discharge Cost Analysis of Real Cases: double membrane technology how to make a plating plant “back from the dead”?
Background: a medium-sized electroplating plant due to environmental protection standards are not met by the production restrictions, the daily discharge of 150 tons of wastewater, nickel concentration of 50mg / L, the traditional precipitation treatment costs up to 550,000 yuan / year.
Solution:
1. Deploy dual membrane separation equipment, supporting ultrafiltration + reverse osmosis system.
2. Recovery of nickel salt for electroplating solution preparation, reducing raw material procurement.
3. Produced water reuse rate of 85%, annual savings of 27,600 US dollars tap water costs.
Results:
• Nickel recovery rate increased from 65% to 92%, annual cost savings of 110,400 US dollars.
• Hazardous waste volume reduced by 90%, no more fines for excessive emissions.
• The investment in equipment was recovered in 3 years, and the current annual net income exceeds 1 million yuan.
Ⅳ. Frequently Asked Questions (FAQ): Eliminating Business Concerns
Q1: Is dual-membrane technology suitable for high-concentration wastewater?
✅ Suitable, but pre-treatment is required to reduce COD to below 100mg/L. The concentrate can be reused to the former section. Concentrate can be reused to the previous process to realize closed-loop recycling.
Q2: How often are membranes replaced?
✅ Regular chemical cleaning can prolong the life, anti-pollution membrane is replaced once in 3 years on average, and the cost is only 10% of the initial investment.
Q3: Does zero emission mean “zero hazardous waste”?
⚠️ Strictly speaking, it is “near-zero emission”, the remaining concentrate should be entrusted to qualified units for disposal, but the amount of hazardous waste can be reduced by more than 90%.
🔹 Free Consultation: Submit the wastewater quality report and get the customized dual membrane equipment plan.