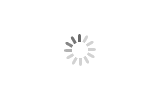
- Qingqingquan
- Shandong, China
- 20 days
- 300 units per month
Zero wastewater discharge in industrial parks is imperative, low-cost technology through four major strategies to achieve cost reduction and efficiency, case studies to verify the feasibility of the future trend to the good
Zero Wastewater Discharge in Industrial Parks: Low-Cost Technologies Pioneering a New Path for Green Transformation
I. Introduction: the urgency and cost challenges of zero wastewater discharge in industrial parks
As the core carrier of high-quality economic development, industrial parks' wastewater discharge problem has become a key bottleneck restricting sustainable development. According to the Ministry of Ecology and Environment, wastewater discharged from industrial parks nationwide accounts for more than 40% of the total industrial wastewater, of which high salt and high COD wastewater accounts for more than 60%. These wastewaters, if discharged directly without effective treatment, will seriously threaten regional water ecological security. The policy clearly requires industrial parks to achieve “zero discharge” of wastewater, forcing enterprises to accelerate technological upgrading.
Core pain points:
• High cost of traditional technology: energy consumption of evaporation and crystallization accounts for more than 40%, and the replacement cycle of membrane system is short;
• Low resource utilization rate: landfill of miscellaneous salts leads to secondary pollution, and there is a lack of high-value recycling path.
Value of the article: put forward “low cost + high resource utilization” dual-objective solution.
Ⅱ. Principle and core process of low-cost zero wastewater discharge technology
(a) Compartmentalized pretreatment technology: the key to extend the life of the membrane
1. Chemical softening in addition to hardness: through the addition of sodium carbonate, sodium hydroxide and other agents, to remove calcium and magnesium ions in the water, to control the hardness of the water at less than 50mg/L, reducing the risk of scaling of the membrane system.
• Case: a power plant in Inner Mongolia uses chemical softening + DTRO membrane concentration process, membrane replacement cycle from 2 years to 5 years, annual cost savings of more than 3 million yuan.
2.Advanced oxidation to break the difficult: the use of Fenton oxidation, ozone catalytic oxidation and other technologies to degrade the difficult to degrade COD, to enhance the efficiency of the subsequent membrane treatment.
• Data: After advanced oxidation treatment in a coal chemical industry park, the COD of wastewater was reduced from 500mg/L to 80mg/L, and the cleaning frequency of membrane system was reduced by 40%.
(b) Gradient Membrane Separation Technology: Precise Separation and Efficiency Improvement
1. Ultrafiltration (UF): retains suspended solids with a particle size ≥0.01μm and protects the reverse osmosis membrane from clogging.
2. Nanofiltration (NF): separates sodium sulfate and sodium chloride, solves the problem of crystallization of mixed salts, and realizes the resourceization of quality crystallization.
3. Reverse osmosis (RO): the conductivity of the produced water is ≤350μS/cm, which can be directly reused in the cooling system, and the recovery rate of fresh water reaches more than 85%.
(c) Comparison: traditional multi-effect evaporation energy consumption 120kWh/t water, MVR evaporation energy consumption only 40kWh/t water, energy saving 67%.
Evaporation crystallization resource technology: turning waste into treasure
1. MVR evaporator: recovering latent heat of secondary steam through mechanical vapor recompression technology, energy consumption is reduced by more than 60% compared with traditional evaporation.
2. Compartmentalized crystallization process: produce industrial-grade sodium chloride and sodium sulfate with purity ≥97%, which can be used in dyeing and printing, glass and other industries instead of primary salt.
• Benefits: A chemical park recovers 18,000 tons of sodium sulfate and 23,000 tons of sodium chloride annually, and the proceeds from the sale of crystallized salt offset 30% of the treatment cost.
Ⅲ. Low-cost technology to achieve path: four major cost reduction strategies
(a) Process optimization cost reduction: heat recovery and quality separation and reuse
1. Heat recovery: use of waste heat from evaporation and crystallization to heat water, reducing steam consumption by 15%-20%.
2. Separate quality reuse: prioritize the use of recycled water in low water quality demand areas such as cooling water and rinse water, reducing fresh water consumption by more than 30%.
(b) Equipment innovation to reduce costs: high-performance materials and long-life design
1. Open flow RO membrane: anti-pollution ability to improve 3 times, cleaning frequency reduced by 50%, life extended to 5 years.
2. Titanium alloy heat exchanger tube: withstand Cl- concentration over 100,000mg/L, life expectancy extended to 30 years, reducing equipment replacement costs.
(c) Resource Recovery and Efficiency Creation: Dual Recovery of Salt and Thermal Energy
1. Salt Recovery: Recovering over 40,000 tons of high-purity salt annually through the fractionated crystallization process, creating an additional revenue of 8 million RMB.
2.Thermal power generation: the high drop wastewater adopts a hydroelectric power generation device, and the annual power generation meets 10% of the system's energy consumption demand.
(d) Intelligent operation and maintenance to reduce costs: online monitoring and predictive maintenance
1. Online monitoring system: real-time monitoring of conductivity, COD and other indicators, automatically adjusting the dosage of pharmaceuticals, reducing manual intervention.
2. Predictive maintenance: Early warning of equipment failure through vibration and temperature sensors, reducing unplanned downtime losses by more than 20%.
Ⅳ. Future Trends: Evolutionary Direction of Low-Cost Technologies
1. Material Innovation: New separation technologies such as forward osmosis (FO) membranes and membrane distillation (MD) will further reduce energy consumption and break through the concentration limitations of traditional membrane separation.
2. Process Integration: Bio-enhanced + membrane separation + evaporation crystallization coupling process to achieve efficient synergistic removal of organic matter, salts, heavy metals.
3. Policy dividend: green credit, tax incentives and other policies will reduce the cost of enterprise transformation, and promote the popularity of low-cost technology to more than 60%.
V.Conclusion: low-cost zero discharge, the green transformation of industrial parks must be
Low-cost zero wastewater discharge technology has entered the “scale application” stage from “proof of concept”. Through process optimization, equipment innovation and resource recycling, industrial parks can achieve a win-win situation in terms of environmental and economic benefits.