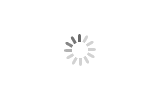
- Qingqingquan
- Shandong
- 20 days
- 300 units per month
Industrial reverse osmosis membrane maintenance needs to control the daily monitoring, regular maintenance, troubleshooting and full-cycle management to improve stability, extend the life of the membrane and realize efficient water use.
Maintenance Guide for Industrial Ro Membranes
Industrial reverse osmosis (RO) membrane is the core component of the water treatment system, and its performance directly affects the water quality and system stability. However, membrane contamination, physical damage and improper operation and other problems easily lead to a decline in water production, increased energy consumption and even membrane element scrap. In this paper, from routine maintenance, regular maintenance, troubleshooting and life extension of the four major dimensions, systematic elaboration of industrial reverse osmosis membrane maintenance points, to provide enterprises with the operation of the program can be landed.
I. Daily maintenance: prevent pollution and guarantee basic performance
1.1 Strictly monitor the quality of incoming water
• Core indicators: control the incoming water SDI (pollution index) <3, residual chlorine <0.1ppm, turbidity <0.2NTU, to avoid irreversible damage of colloid, microorganisms and oxidizing substances to the membrane.
• Pre-treatment optimization: configure multi-media filter, activated carbon filter and security filter according to the water quality characteristics, backwash or replace the filter media regularly to ensure that the pre-treatment efficiency is ≥98%.
1.2 Standardize the management of operating parameters
• Pressure control: maintain the inlet water pressure within ±10% of the rated value of the membrane element to avoid overpressure leading to membrane deformation or desalination layer stripping.
• Flow balance: Ensure that the ratio of concentrated water flow to produced water flow meets the design requirements (usually 3:1-5:1) to prevent scaling on the concentrated water side.
• Temperature management: control the feed water temperature at 20-30 ℃, every 1 ℃ increase in temperature, the membrane flux increased by about 3%, but more than 35 ℃ will accelerate membrane aging.
1.3 Real-time data recording and analysis
Establish an operation log to record key parameters such as pressure, flow rate, conductivity, etc., and discover the risk of membrane contamination or system leakage in advance through trend analysis.
Example: If the conductivity of produced water suddenly rises by 20%, it may indicate that the membrane is broken or O-ring leakage, and it needs to be shut down immediately for inspection.
II. Regular maintenance: deep cleaning, restore membrane performance
2.1 Chemical cleaning cycle and program
Cleaning timing: when the standardized water production decreased by 10% -15%, the differential pressure increased by 15% -20% or desalination rate decreased by 5%, the need to start chemical cleaning.
Cleaning agent selection:
• Acid cleaning: for inorganic scale (e.g. CaCO₃, BaSO₄), use 1%-2% citric acid or hydrochloric acid solution, with pH control at 2-3.
• Alkaline cleaning: for organic or biological pollution, use 0.1%-0.5% NaOH+0.1% SDS solution, with pH control at 11-12.
• Cleaning process: low flow rate Cycling → immersion → high-flow rinsing, a single cleaning time of no more than 4 hours, to avoid hydrolysis of membrane materials.
2.2 Physical Cleaning Auxiliary Means
• Backwashing: 10-15 minutes of backwashing is carried out during daily shutdown to remove loose pollutants on the membrane surface.
• Air scrubbing: for hollow fiber membrane, oil-free compressed air (pressure ≤ 0.1MPa) can be passed through the vibration cleaning to enhance the effect of pollutant stripping.
2.3 Shutdown protection measures
Short-term shutdown (<48 hours): low-pressure flushing once a day to prevent microbial growth.
Long-term shutdown (>48 hours):
• Membrane elements are immersed in 1% sodium bisulfite solution to inhibit bacterial reproduction.
• Periodically circulate the protective solution to avoid membrane drying or icing (temperature ≥5℃).
III. Troubleshooting: Quick Response to Reduce Losses
3.1 Common Troubles and Solutions
3.2 Emergency treatment process
• Immediate shutdown: close the water inlet valve and water production valve to prevent further spreading of pollutants.
• Pressure relief and drainage: open the thick water discharge valve and reduce the system pressure to below 0.1MPa.
• Isolate the faulty section: Isolate the problem membrane element through the bypass valve to restore part of the system capacity.
• Professional overhaul: Contact membrane supplier or service provider for in-depth diagnosis and repair.
IV. Extend the life: full-cycle management strategy
4.1 Membrane element selection and matching
According to the quality of incoming water, select anti-pollution membrane (such as FR membrane) or high desalination rate membrane (such as BW30HR), to avoid “small horse-drawn cart” leading to premature failure.
Example: High hardness water should be prioritized to use anti-scaling membrane, reduce the frequency of chemical cleaning.
4.2 Operator training and assessment
Regularly organize membrane system operation training, focusing on the assessment of parameter adjustment, cleaning operation and fault identification ability.
Establish an assessment mechanism to link the membrane life and operator performance to strengthen the sense of responsibility.
4.3 Construction of digital operation and maintenance platform
Deploy SCADA system to monitor the operating status of the membrane system in real time and predict the trend of membrane contamination through AI algorithm.
Example: A chemical enterprise extends the membrane cleaning cycle from 3 months to 6 months through a digital platform, saving over 500,000 yuan in annual costs.
Conclusion
The maintenance of industrial reverse osmosis membrane needs to run through the whole cycle of design, operation and maintenance, and the system stability and economy can be significantly improved through refined management and technological innovation. Enterprises should combine their own water quality characteristics and process requirements, develop personalized maintenance programs, and continue to optimize the operation process, in order to achieve the dual goals of maximizing the life of membrane elements and efficient use of water resources.