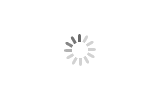
- Qingqingquan
- Shandong
- 20 days
- 300 units per month
Discover why 65% of biopharma companies are switching from distillation to RO+UF+UV for WFI production. Learn FDA/EMA standards, cost-saving case studies & compliance tips.
Pharmaceutical Grade Sterile Water Production System: FDA Compliant WFI Solution
In the biopharmaceutical field, the quality of water for injection (WFI) is directly related to drug safety. As FDA and EMA regulations become more stringent, traditional distillation processes are gradually being replaced by the innovative combination of Reverse Osmosis (RO) + Ultra Filtration (UF) + UV. In this article, we will analyze the pharmaceutical water standards and share the successful practice cases of vaccine companies.
I. Analysis of international standards for pharmaceutical water
1. Stringent requirements for microorganisms and endotoxins
• USP<1231> standard: microbial content needs to be <10 CFU/100ml
• Endotoxin control: ≤0.25 EU/ml (European Pharmacopoeia more stringent to ≤0.03 EU/ml)
• TOC limit: <500 ppb
Industry data: 35% of Form 483 issued by FDA in 2023 related to water system related defects.
2. Conductivity and Chemical Composition Requirements
• Conductivity: ≤1.3 μS/cm @ 25°C
• Heavy metals: lead, cadmium and other content needs to comply with ICH Q3D standards
II. Modern WFI production technology
1. Reverse osmosis (RO) system
• Removes more than 99% of ions and small molecules of organic matter.
• Sanitary 316L stainless steel membrane shell to avoid contamination.
2. Ultra Filtration (UF) technology
• Retains endotoxins with molecular weight >10kDa.
• Pyrogen removal efficiency >99.9%.
3. UV sterilization system
• 254nm UV lamp: inactivate microorganisms
• 185nm UV Lamp: Degradation of TOC
Process Comparison Table:
Technology | Treatment object | Efficiency |
---|---|---|
RO | Ion/small molecule | >99% |
UF | Endotoxin | >99.9% |
UV | Microorganisms | >99.99% |
III. Successful case: vaccine company's efficiency increased by 50%
1. Project background
A multinational vaccine producer was faced with:
• High energy consumption of traditional distillation process
• Water production cycle up to 8 hours / batch
• Difficult to meet the demand for production expansion
2. Solution
• adopts modularized RO+UF+distillation combination system
• Equipped with online TOC monitor
• Realize full automation control
3. Achievements
✅ Shortened water production cycle to 4 hours
✅ Reduced operating costs by 40%
✅ Passed FDA on-site inspection
IV. Industry Trend: CDMO Driving Demand for Modularization
1. Market Growth
• Global CDMO Market Size is Expected to Reach USD 23.8 Billion by 2025
• China's biopharmaceutical companies annual growth rate of more than 20 percent
2. Advantages of Modularization
• Short construction cycle: 60% faster than traditional systems
• Flexible expansion: supports gradual capacity increase
• Access to customized solutions