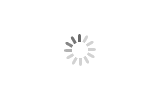
- Qingqingquan
- Shandong
- 20 days
- 300 units per month
See how a dyeing factory achieved zero discharge (5000T/day). Compare technologies & costs. Request your wastewater assessment today.
Zero Discharge Solution for Textile Printing and Dyeing Wastewater: 90% Reuse Rate Technical Guide
I. Water Treatment Challenges Facing the Textile Printing and Dyeing Industry
1. Characteristics of Printing and Dyeing Wastewater and Treatment Difficulties
Textile Printing and Dyeing Wastewater has the following characteristics, which make it a difficult problem in industrial wastewater treatment:
• High color: the complex molecular structure of dyes is difficult to be degraded by traditional methods.
• High COD: chemical oxygen demand usually reaches 3000-5000mg/L.
• High salinity: Salt content exceeds 10,000mg/L, which corrodes the equipment.
Latest policy: China's "14th Five-Year Plan" clearly requires that the water reuse rate of printing and dyeing industry shall not be less than 45% by 2025.
2. The limitations of traditional treatment methods
• Conventional biochemical treatment COD removal rate of only 50-60%
• Simple physical filtration can not remove dissolved pollutants
• High sewage charges increase the burden of enterprises
Ⅱ. Zero discharge core technology: RO+MBR combination process
1. Tertiary treatment process
Pre-treatment stage:
• Ozone oxidation destroys the molecular structure of dyes
• Coagulation and precipitation to remove suspended solids
MBR membrane bioreactor:
• PVDF ultrafiltration membrane, pore size 0.1μm
• COD removal rate up to 95% or more
Reverse osmosis fine treatment:
• Disc tube RO (DTRO) treatment of concentrated water
• Final reuse rate of up to 90
Technology Comparison Table:
Treatment Process | COD Removal Rate | Investment Cost (USD/ton) | Operating Cost (USD/ton) |
---|---|---|---|
Traditional Biochemical | 60% | 0.11 | 0.17 |
MBR | 85% | 0.21 | 0.28 |
RO + MBR | 95% | 0.42 | 0.35 |
Ⅲ. Successful cases: a large-scale printing and dyeing plant renovation project in Zhejiang Province
1. Project background
• Daily discharge: 5000 tons
• Raw water COD: 3200mg/L
• Facing the risk of environmental fines of 390,600 USD
2. Solution
• Installation of ozone oxidation system
• Configure 1000m³/d MBR device
• Adopt DTRO to treat concentrated water
3. Implementation effect
✅ Water reuse rate increased to 92%
✅ Save 1.46 million tons of water per year
✅ Save 601,300 USD/year
✅ Selected as "National Green Factory".
Ⅳ. Market Opportunities and Policy Orientation
1. China's Environmental Protection Policy is Tightening
• Zhejiang, Guangdong and other key provinces require the completion of renovation before 2025.
• Emission license system promotes enterprise upgrading
2. Southeast Asia market opportunities
• Vietnam, Indonesia and other emerging textile bases demand growth
• Layout in advance to seize the market opportunity
V. Key elements of system selection
1. Core equipment selection criteria
• MBR membrane module: PVDF material, flux>15LMH
• RO system: high-pressure resistant DTRO membrane, anti-pollution
• Control system: online monitoring COD / conductivity
2. Investment return analysis
• Typical project payback period: 3-5 years
• Long-term operating costs reduced by 30-40%
Get professional solutions